How We Work
Moldie Die Casting’s engineers have extensive experience designing durable, low-maintenance molds. We believe that great mold design is the key to casting success. To get started on your project:
1. Send us your 2D/3D drawings or sample parts
2. We’ll generate a detailed product blueprint for your review
3. Once you approve the blueprint, we begin designing your custom mold
We accept common file formats including: DXF, DWG, IGES, STEP
If you provide physical samples, we can also 3D scan them to create the initial design. Throughout the design process, we use advanced CAD/CAM/CAE software to seamlessly integrate your exact specifications. This allows us to deliver a precision mold that matches your requirements. With Moldie’s expert engineering and state-of-the-art technology, you can trust us to bring your die casting project to life. Contact us today to discuss your mold design needs.
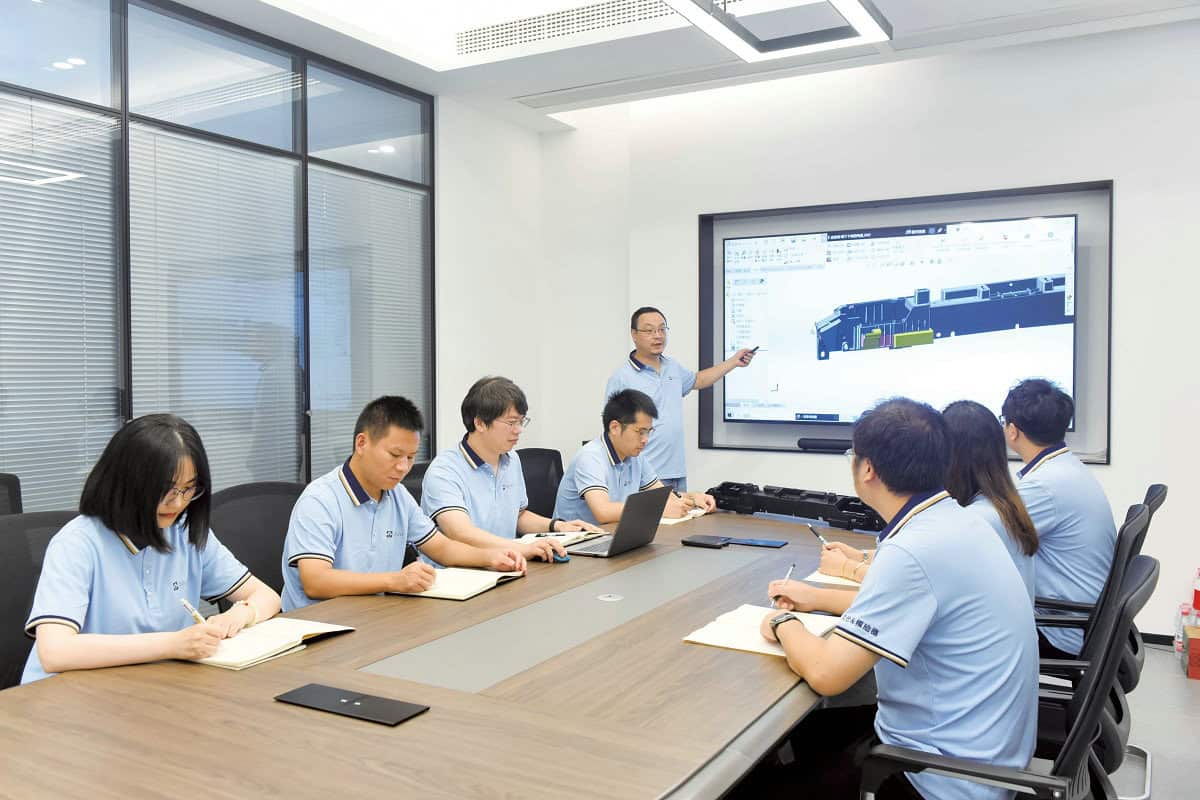
Mold Production Process
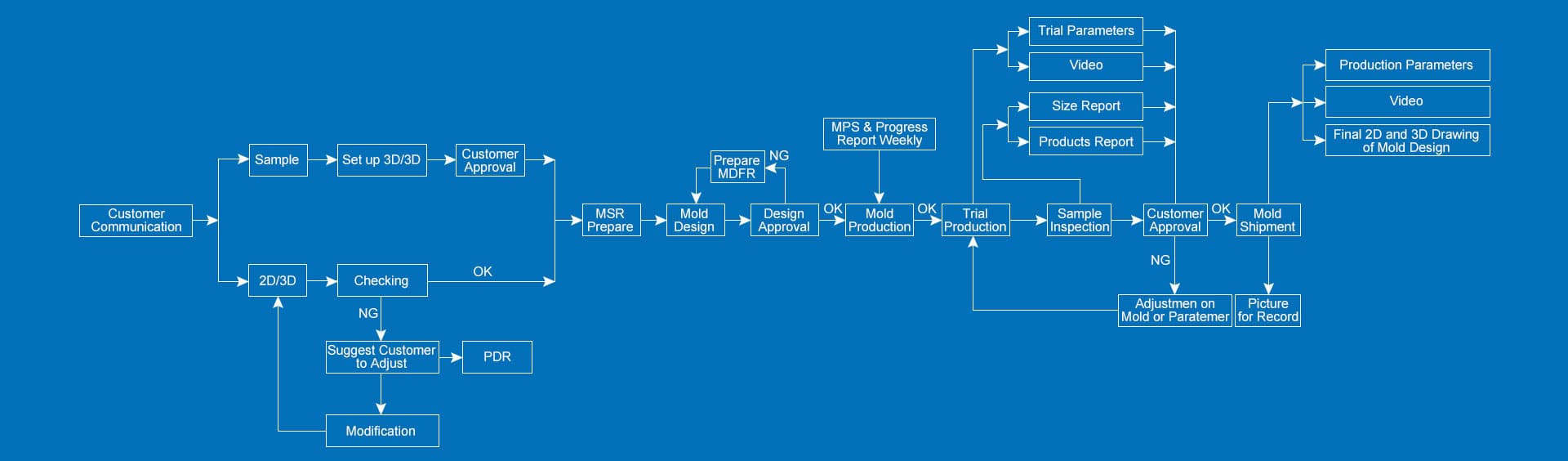
Quality Management
Testing equipment is an indispensable means of guaranteeing the mold manufacturing process. A high-quality quality management team with precise testing equipment is the guarantee for creating high-quality molds. The quality inspection department is equipped with two high-precision three-coordinate and 3D scanners. We promise to issue a full-size report within three days after the product trial, and a 3D scan report within two days.
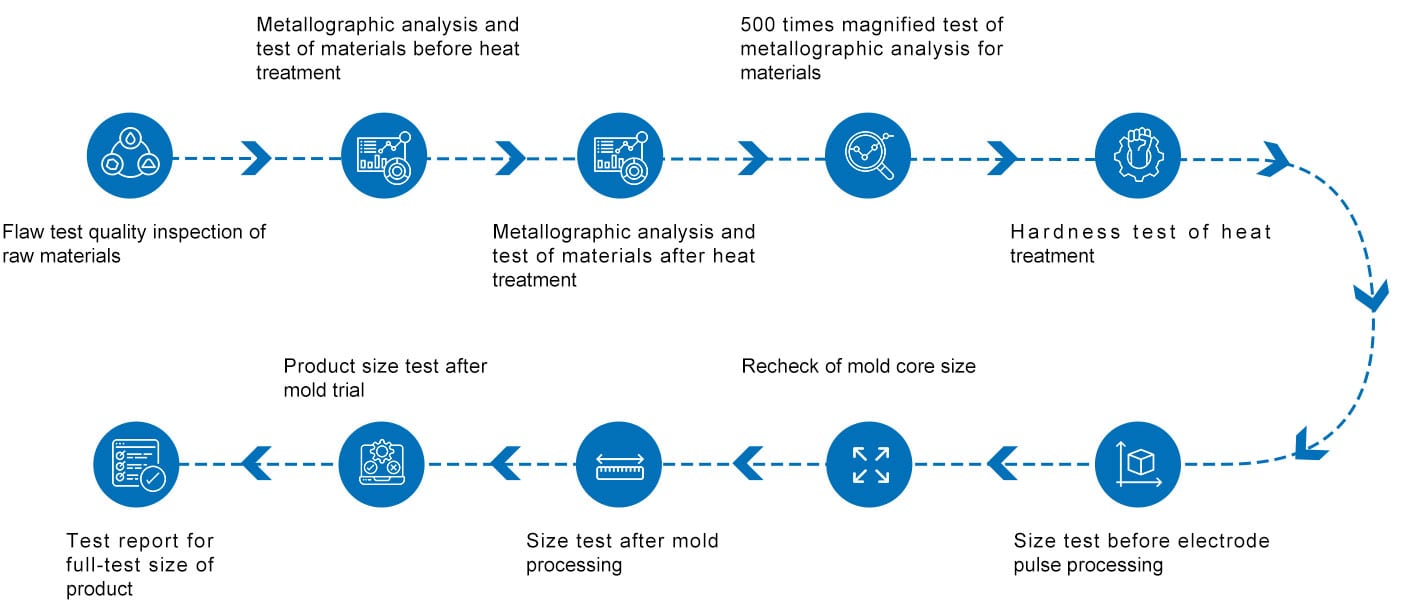
Mold Flow Analysis
Moldie Engineering Center consists of more than 30 engineering and technical personnel. lts also the technical center certified by Zhejiang Province. The technical center possesses the most professional personnel for plastic injection, non-ferrous, ferrous engineering, mold structure design with software UG.PRO/E, CIMATRON, LK/DIMS5.5, METRIS SCCAN4.2 in order to engineering, design simulation, machining, inspection to support and guarantee the quality and function the tooling we constructed.
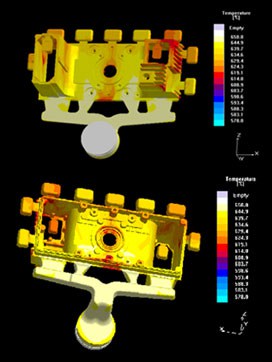
Temperature distribution analysis
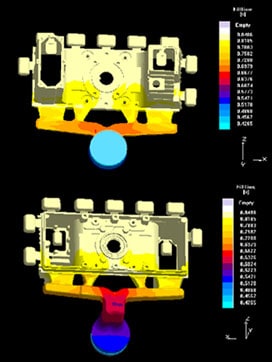
Fill time analysis
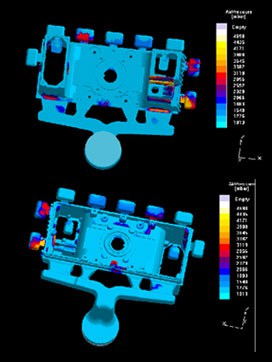
Air pressure result
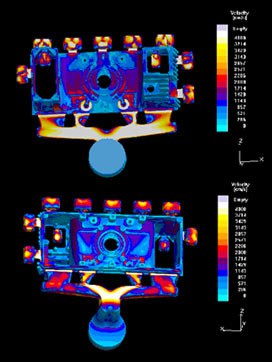
Filling velocity Analysis

Shrink Hole Analysis
Die-casting Production
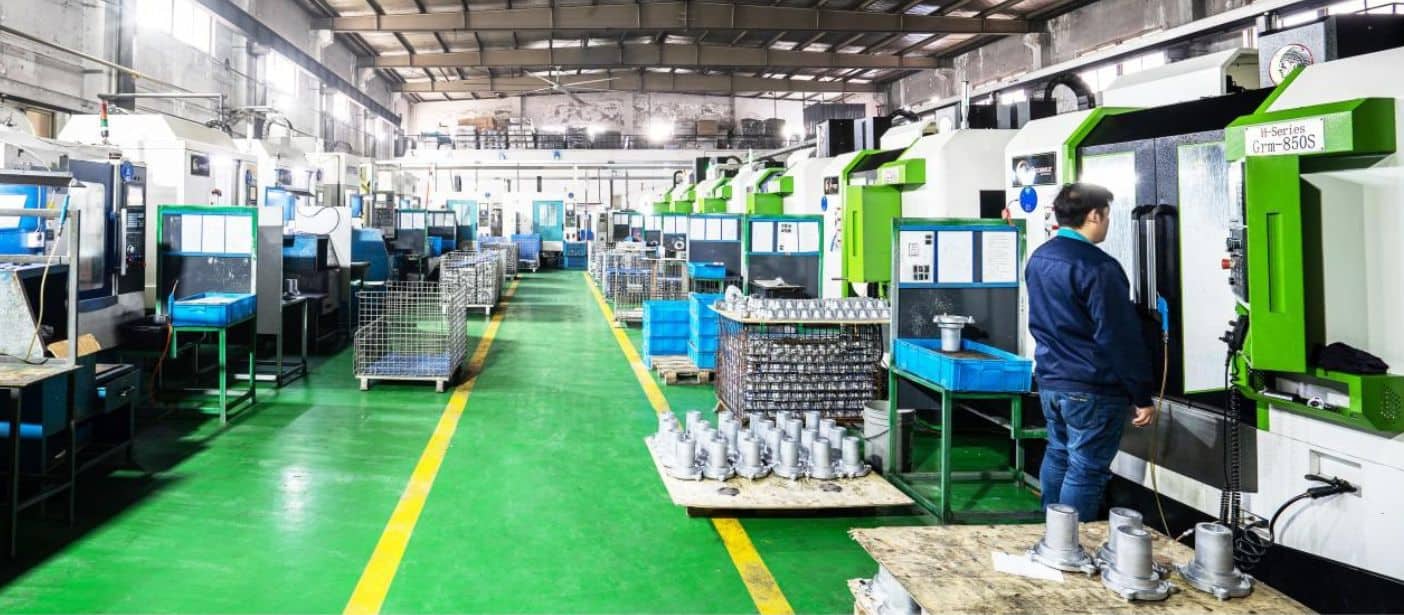
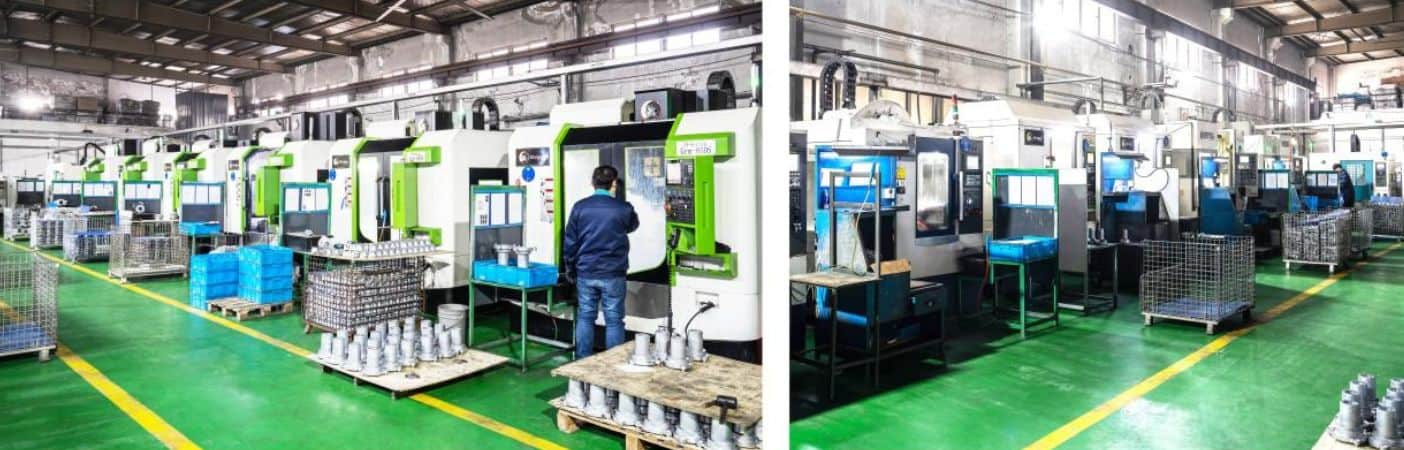